Drawing and Roving in Cotton Spinning: Technology, Impact, and Final Yarn Quality
- Bidco International
- Apr 6
- 3 min read
Updated: 3 days ago
Introduction:
Cotton spinning is a vital industry that heavily relies on the accuracy and integration of various production stages, from fiber preparation to the final yarn. Among these stages, drawing and roving stand out as critical processes that directly influence yarn quality and its physical characteristics. It is impossible to produce high-quality cotton yarns without precise control over the properties of slivers and rovings produced in these two steps. This article highlights the importance of drawing and roving in producing homogeneous yarns with distinctive specifications and reviews the latest technological developments in this field.
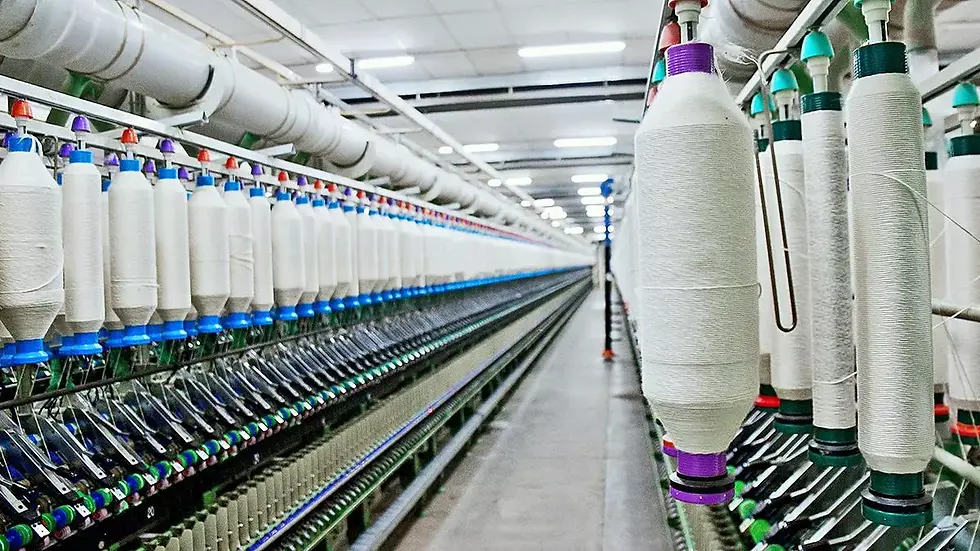
1. Drawing:
Drawing is the process in which raw slivers from the carding stage are treated to improve their uniformity and reduce thickness variations. This is achieved by passing multiple slivers through a series of rollers rotating at graduated speeds. These rollers stretch the slivers and align the fibers more uniformly, resulting in a sliver that is consistent in mass and length, which directly affects the stability of the yarn properties in later stages.
Machines used in this process include the first and second draw frames, which combine several parallel slivers into a single, more uniform one. These machines are equipped with precise pressure systems and sensors to detect irregularities in real-time, allowing immediate adjustments. Proper control of the drawing process contributes to a significant reduction in mass variations and enhances fiber distribution—factors that visibly improve the final yarn’s smoothness and stability during further processing.
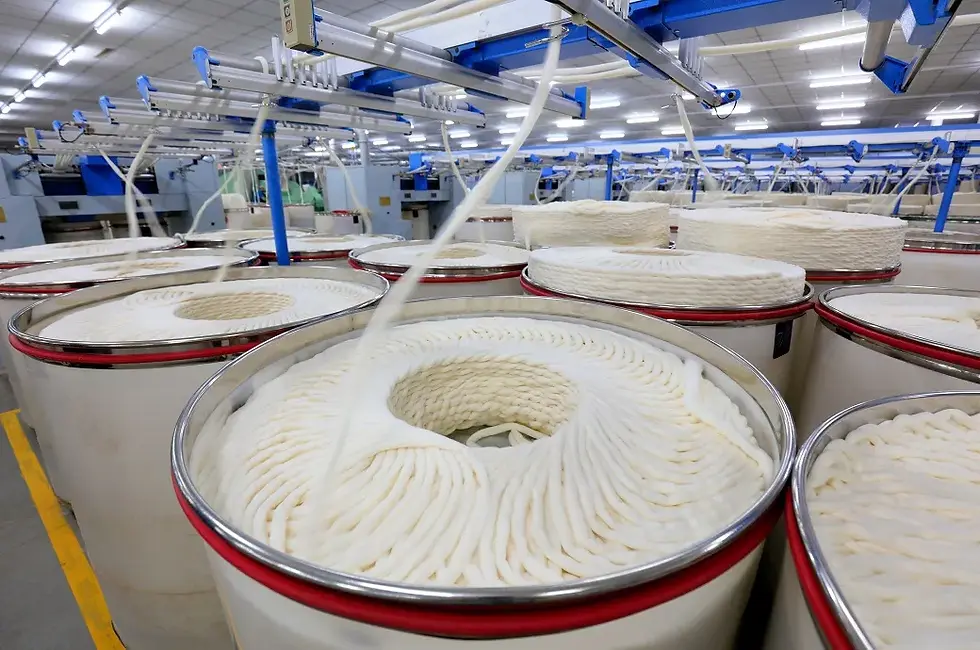
Roving:
Following the drawing stage, roving serves as a transitional process where the drawn sliver is converted into a finer strand (roving) with slight twist to ensure fiber cohesion and prepare it for final spinning. This step requires meticulous control over tension and twist, as even minor deviations may lead to weak yarn or inconsistent twist levels.
Roving is carried out using the Simplex machine, which feeds the sliver while imparting a light twist through a rotating mechanism and simultaneously controlling drafting and winding speeds. The resulting roving is the foundation for ring spinning, and any irregularities in its tension or cohesion will directly affect the final yarn quality—both in terms of strength and appearance.
Modern Technologies: Recent years have seen remarkable advancements in spinning technology, particularly in automating the drawing and roving stages. Today’s machines often rely on PLC-based systems for fine-tuned control of drafting parameters and tension. They also employ laser-based sensors to continuously monitor sliver or roving uniformity.
Some factories have begun integrating AI-driven systems to analyze real-time production data and suggest immediate process optimizations. These advancements also extend to integration with ERP systems, enabling full traceability of each machine’s output and its impact on final yarn quality.
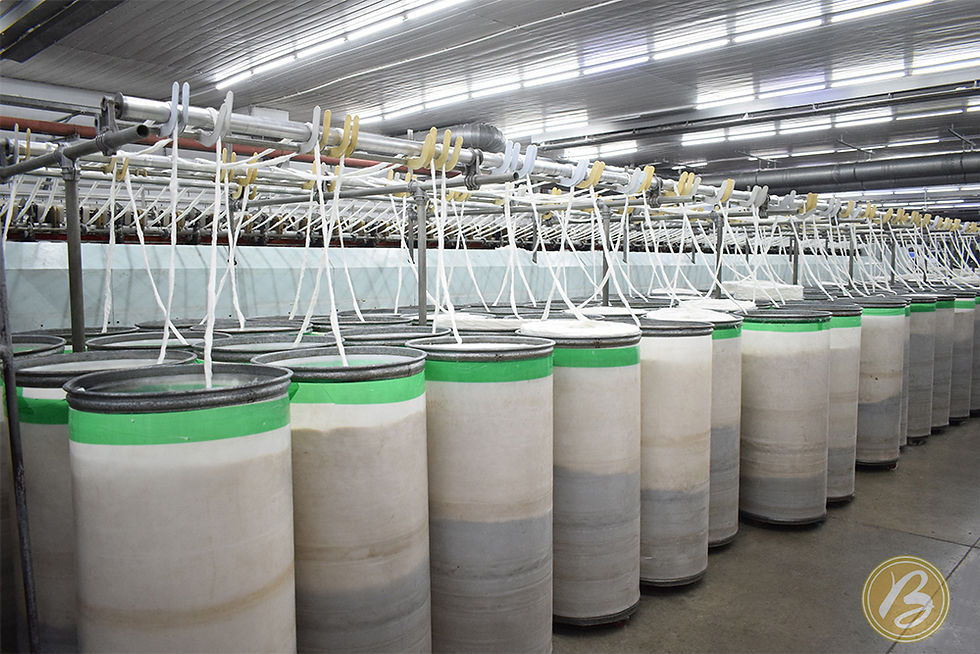
The Impact on Yarn Quality:
The efficiency of the drawing and roving processes directly determines the quality of the final yarn. Uniform slivers result in yarns that are consistent in thickness and weight. Furthermore, minimizing free fibers during drawing leads to smoother, stronger yarns with superior appearance.
During roving, precise control over twist and feed rate ensures cohesive rovings, which in turn provide stable yarns during ring spinning and easier handling during weaving or knitting. Enhancing both processes leads to improved production efficiency, reduced waste, and better-quality end products.
Common Errors: Typical issues in the drawing stage include improper settings of roller speed differentials, causing uneven fiber elongation and sliver inconsistency. Excessive pressure can also damage fibers or raise temperatures, weakening the final product.
In the roving stage, fluctuating tension or poor fiber distribution can lead to roving breakage or inconsistent twist, resulting in weak spots or diameter variations in the yarn. These defects are unacceptable in high-quality textile applications.

Future Trends: The industry is moving toward more integrated production lines where drawing, roving, and spinning are combined into a single synchronized unit. This reduces processing time and waste while boosting overall efficiency.
Industry 4.0 technologies are expected to play a key role in real-time monitoring and optimization of every production stage. Predictive maintenance and continuous process analytics are now being explored to prevent defects before they occur. There is also growing interest in recycling short fibers from the spinning process and utilizing them in innovative ways to enhance raw material efficiency.
Conclusion:
Drawing and roving are the heartbeat of cotton spinning, playing a crucial role in defining the final yarn's characteristics. With technological advancements, it is now possible to control every parameter of these processes with high precision, opening new opportunities for improved quality and productivity. In-depth knowledge of these stages is essential for any specialist aiming to develop competitive yarn products in both local and global markets.
Comments