From Tangled Fibers to Smooth Threads: The Evolution of Carding and Combing Techniques Through the Ages
- Bidco International
- Mar 25
- 3 min read
Updated: Apr 6
Introduction
Carding and combing are crucial processes in cotton spinning, serving as the primary steps in transforming raw cotton fibers into smooth, uniform threads used in fabric production. With advancements in industrial technology, these processes have evolved from manual labor to highly sophisticated mechanical systems that enhance yarn quality and increase production efficiency. This article explores the evolution of carding and combing techniques from ancient times to the modern era, shedding light on the mechanics behind these processes and the latest technologies employed today.
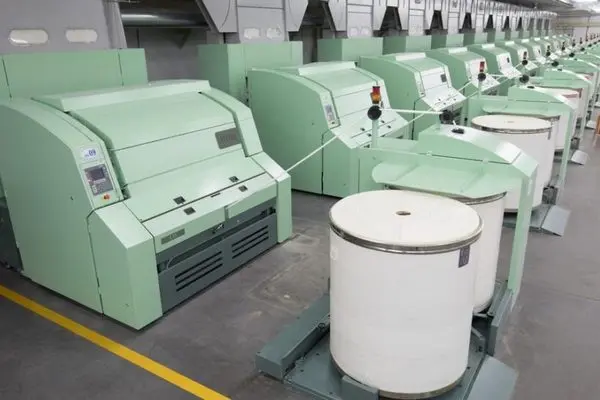
1. Carding and Combing: The Differences and Their Importance
Carding:
Carding is the first step in fiber preparation, where clumps of cotton fibers are separated and aligned using rollers covered with fine metallic teeth. The primary goal of this process is to arrange the fibers in a parallel direction while removing impurities and residual seeds.
Combing:
Combing follows carding and is an optional process used to achieve exceptionally fine and high-quality yarns. This stage removes short fibers (less than 15 mm in length), which affect the final yarn quality. This technique is used in producing premium fabrics such as Egyptian cotton and American Pima cotton.
2. The History of Carding and Combing: From Hand Tools to Industrial Machines
Ancient Times
In ancient civilizations, cotton was combed manually using wooden combs with sharp teeth to separate fibers from seeds. Cultures such as the Egyptians and Indians relied on these methods, using combed cotton for royal garments.
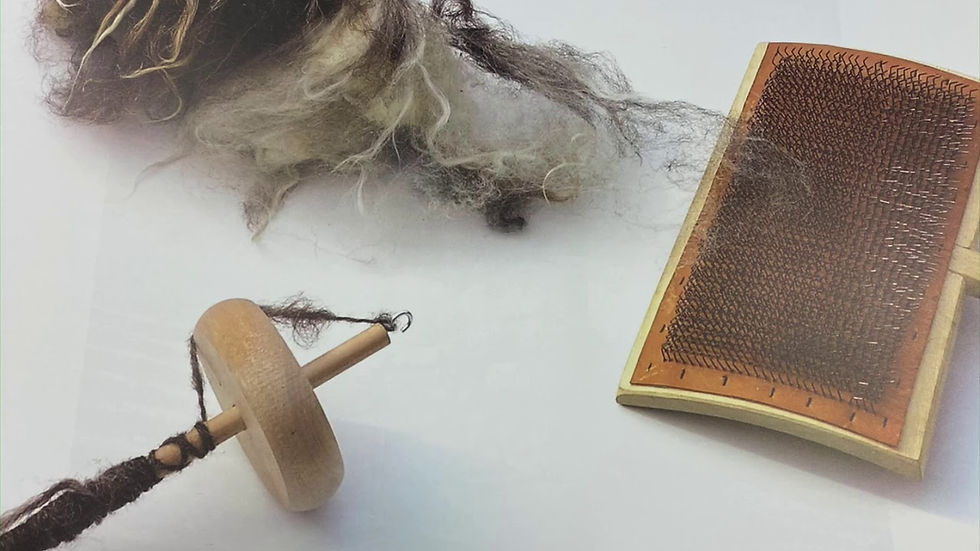
The Industrial Revolution (18th and 19th Centuries)
During the Industrial Revolution, the first carding machines emerged in Britain in the mid-18th century. One of the most significant inventions was Richard Arkwright's carding machine in 1775, which paved the way for a revolution in the textile industry.

The 20th Century: The Era of Automation
By the 20th century, carding and combing technologies had evolved significantly with the introduction of electricity and automated control systems in production lines. This period saw the development of combing machines capable of producing yarns with diameters as fine as 20 micrometers, greatly improving cotton product quality.
3. Modern Technologies in Carding and Combing
A. Advanced Carding Machines
Modern carding machines use multiple rollers operating at different speeds, allowing for the processing of over 100 kg of fibers per hour. These machines incorporate technologies such as:
Continuous fiber feeding: Reducing waste and increasing efficiency.
Digital quality monitoring: Using sensor systems to detect impurities or defects in fibers.
B. Intelligent Combing Systems
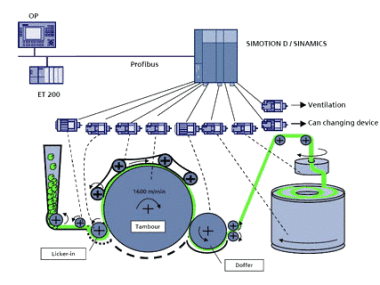
Today, artificial intelligence is utilized in combing systems to analyze fiber quality and select the best fibers for spinning. Modern combing machines can reduce the percentage of short fibers by 40-50%, ensuring stronger and more dye-resistant yarns.
C. Compact Spinning Technology
In some cases, combing can be bypassed using technologies like "compact spinning," which rearranges fibers during drafting to minimize defects and increase yarn density.
4. The Economic and Environmental Impact of Carding and Combing Advancements
Increased productivity: The development of carding and combing technologies has doubled production in spinning mills, with some factories processing over 5,000 kg of cotton daily.
Reduced waste: Modern advancements have reduced raw cotton waste from 30% to less than 10%.
Enhanced environmental sustainability: With the industry's shift towards renewable energy, carding and combing operations have become more eco-friendly, lowering electricity and water consumption in modern mills
Conclusion
From ancient times to the present day, carding and combing processes have undergone remarkable advancements, making it possible to produce superior-quality cotton fabrics thanks to continuous technological innovations. With the integration of artificial intelligence and digital systems in spinning, the future holds even more improvements, ensuring cotton products that are softer, more durable, and more sustainable.
Kommentare